Metallised plastic films have traditionally been hard to recycle as the metallic content isn’t separated from the polymer, meaning it’s not reusable. This often leads to metallised films being discarded as waste. However, in a joint project, GMS Plastic Machinery Private Limited and JPFL Films Private Limited in Mumbai, India, have found an innovative solution.
The project team developed a special food-grade detergent and added it to the washing process for plastic films metallised on one side. The detergent softened the metallised coating, and thanks to the friction of the washing equipment, 100% of the softened metallised coating could be removed, leaving a clean polymer that could be reused, including for food packaging.
“Innovation is a core requirement in our business to stay ahead of competition and save the Environment.”
GMS Technical Team
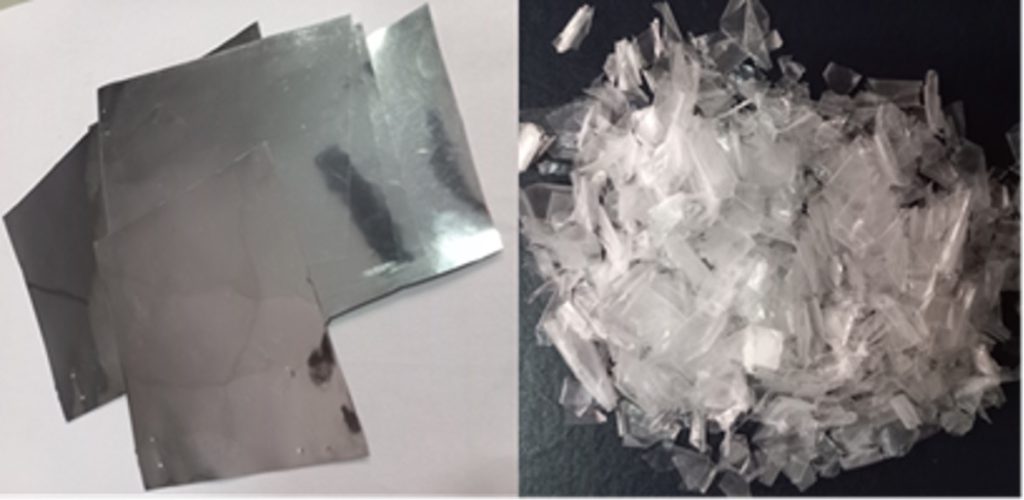
Recycling reaps rewards
Thanks to this novel approach, the manufacturer could recover 100% of the production waste which was metallised but rejected during production due to flaws. The process enabled the films to be recycled to make the same film again and metallise it or print it for various applications, reducing the need for raw materials while being cost-effective and repeatable.
Total raw material saving = 100%
Total process cost = INR. 12/- per kgs of polymer weight
The project has delivered several clear benefits:
- Circular economy: creating recycled films equivalent to virgin material quality so they can be reused to make new films
- Very low cost: the washing of the waste was incorporated into the overall process, reducing the need and cost of multiple operations
- Efficient results: 100% of the metallised coating was removed from the film, creating a polymer that could be reused
- Recovery cost: recovery of the film waste back to the same film helped to reduce waste that needed to be disposed of
- Food gradeability: The ingredients used in the detergent were non-toxic. The recycled film and its granules were tested as food-grade – just like virgin granules
Benefitting the environment and the bottom line
Adopting an in-house recycling process reduces the impact on the environment from transportation movements, use of raw materials and waste creation. Additional positive benefits include:
- Environmental impact: The project aims to reduce plastic waste, promote recycling practices, and effectively lower the film’s carbon footprint.
- Economic impact: An in-house solution that reduced the cost of transporting waste materials that were previously sold, while 100% of the waste was recycled into the same produce, meaning there was less need for new raw materials.
- Social impact: The project has positively impacted the environment and society by introducing an innovative waste processing solution.
“Providing customised solutions makes GMS the best recycling solutions provider.”
GMS Marketing Team